Siemens – Siemens to acquire industrial drive technology business of ebm-papst
- Planned acquisition to strengthen Siemens’ position as a leading technology company in the field of factory automation and digitalization
- Strategic addition to the Siemens Xcelerator portfolio
- A business of ebm-papst, a leading supplier of fans and compact and intelligent mechatronic systems, which employs around 650 people
- Major growth opportunities in the field of intelligent, battery-powered drive solutions
Siemens AG has signed an agreement to acquire the industrial drive technology (IDT) business of ebm-papst. The business, which employs around 650 people, includes intelligent, integrated mechatronic systems in the protective extra-low voltage range and innovative motion control systems. These systems are used in free-range driverless transport systems. The planned acquisition will complement the Siemens Xcelerator portfolio and strengthen Siemens’ position as a leading solutions provider for flexible production automation.
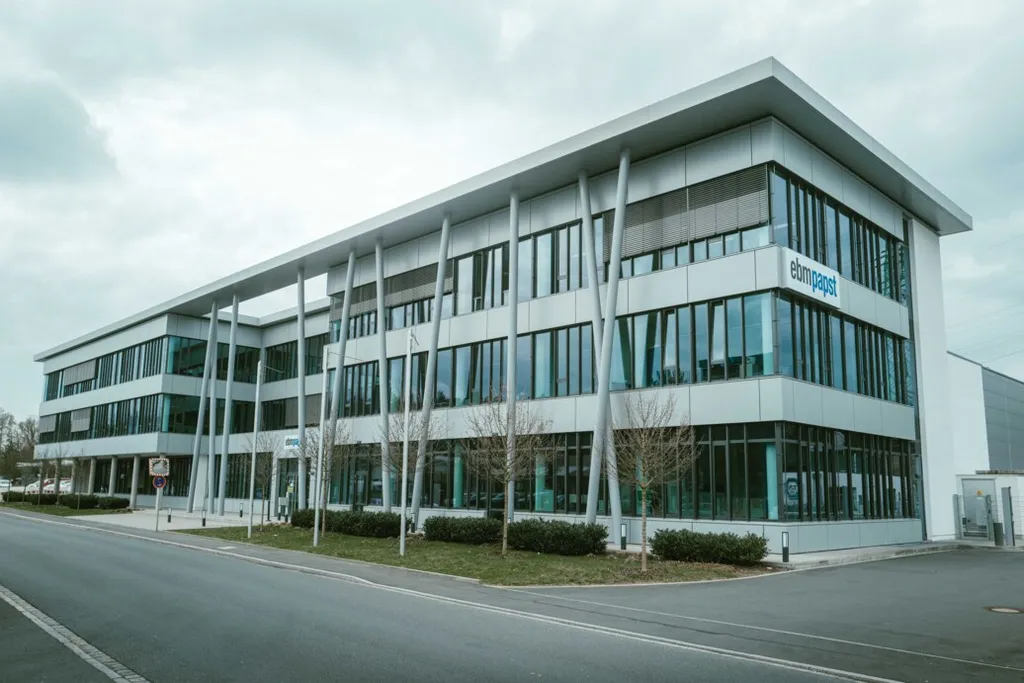
Exterior view of the ebm-pabst facility in Lauf an der Pegnitz, Germany / Copyright: Christof Wolf
Cedrik Neike, member of the Managing Board of Siemens AG and CEO of Digital Industries, said: “Ebm-papst’s innovative portfolio of mechatronic drive systems and its highly qualified people are an excellent fit for Siemens. The acquisition will enable us to tap new business and customer potential in the rapidly growing market for intelligent, battery-powered drive solutions in intralogistics as well as mobile robot solutions.”
IDT products are intelligent, integrated mechatronic systems, which support the automation and digitalization of production processes. This acquisition will be a strong addition to the Siemens Xcelerator portfolio. Through their use in mobile robots and driverless transport vehicles as well as in the automation of auxiliary processes, such as the retooling of modern production machines, they are an important lever for greater flexibility and productivity. For this reason, high market growth is expected in this market segment.
The integration of the IDT portfolio into the existing automation portfolio and the utilization of Siemens’ global sales network will open up new market access and generate significant business potential in the area of flexible and autonomous factory automation.
The transaction is to be completed by mid-2025, subject to the necessary foreign trade and merger control approvals. The IDT business of ebm-papst is located in St. Georgen and Lauf an der Pegnitz, Germany, and in Oradea, Romania. The parties have agreed not to disclose the purchase price.
“The acquisition by Siemens is a strategically significant step for us. What our industrial drive technology (IDT) business had lacked until now was a global sales organization for maximum growth. Siemens is a long-standing customer and a company with strong international market penetration and an extensive customer base. The integration that has now been agreed upon will give our IDT business global market access. It will open up new horizons for innovation and further growth,” added Dr. Klaus Geißdörfer, CEO of the ebm-papst Group. “We’ll use the proceeds from the sale of the IDT business to further expand our Air Technology and Heating Technology divisions, to further strengthen our three regions – Europe, Asia and the Americas – and to invest in future fields of our product portfolio, such as digitalization and sustainability.”
This investment in intelligent, integrated and network-connected mechatronic systems underscores Siemens’ commitment to sustainable innovation and its position as a leading supplier of systems and solutions for future-oriented, flexible production automation.
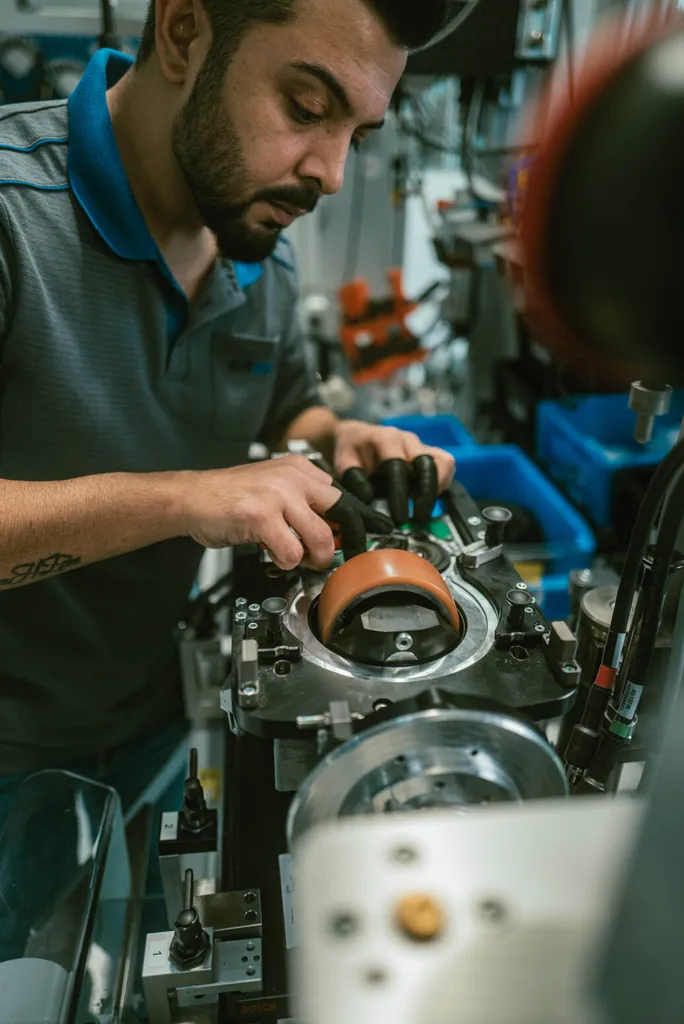
Assembly work at the ebm-pabst facility in Lauf an der Pegnitz, Germany / Copyright: Christof Wolf
SourceSiemens
EMR Analysis
More information on Siemens: See the full profile on EMR Executive Services
More information on Dr. Roland Busch (President and Chief Executive Officer, Siemens AG): See the full profile on EMR Executive Services
More information on Siemens Digital Industries (DI): See full profile on EMR Executive Services + https://new.siemens.com/global/en/company/about/businesses/digital-industries.html + Siemens DI is an innovation leader in automation and digitalization. Closely collaborating with partners and customers, DI drives the digital transformation in the process and discrete industries. With its Digital Enterprise portfolio, DI provides companies of all sizes with an end-to-end set of products, solutions and services to integrate and digitalize the entire value chain. Optimized for the specific needs of each industry, DI’s unique portfolio supports customers to achieve greater productivity and flexibility. DI is constantly adding innovations to its portfolio to integrate cutting-edge future technologies. Siemens Digital Industries has its global headquarters in Nuremberg, Germany, and has around 76,000 employees internationally.
More information on Cedrik Neike (Member of the Managing Board and Chief Executive Officer, Siemens Digital Industries, Siemens AG): See full profile on EMR Executive Services
More information on Xcelerator by Siemens: https://www.sw.siemens.com/en-US/digital-transformation/ + Xcelerator provides the engineering and manufacturing software, services and application development platform to blur the boundaries between industry domains. Companies can use this technology today to build the products of tomorrow. Turn complexity into your competitive advantage with Xcelerator.
Siemens Xcelerator consists of three pillars:
- Portfolio: A curated, modular portfolio of IOT-enabled hardware and software based on standard application programming interfaces, facilitating the integration of information technology (IT) and operational technology (OT).
- Ecosystem: A growing ecosystem of partners.
- Marketplace: Interactions and transactions among customers, partners and developers.
More information on ebm-papst: https://www.ebmpapst.com/de/en/home.html + Your partner for sustainable, intelligent and innovative air and heating technology.
We know how to use air efficiently and intelligently. And we make sure you feel good about it!
Whether it’s air conditioning, data centers, clean rooms, refrigeration, industrial cooling, transport, renewable energy or residential ventilation – you come into contact with our solutions and products every day, at work or at home. If you don’t notice, we’ve done our job well.
More information on Dr. Klaus Geißdörfer (Chief Executive Officer, ebm-papst): https://www.ebmpapst.com/de/en/company/about-ebm-papst.html + https://www.linkedin.com/in/klaus-geissdoerfer-39a131/
EMR Additional Notes:
- Industrial Automation:
- Industrial automation is the use of technologies such as computer software and robotics to control machinery and processes which replace human beings in performing specific functions. The functions are primarily centered on manufacturing, quality control and material handling processes.
- Fixed Automation:
- Fixed automation systems are utilized in high volume production settings that have dedicated equipment. The equipment has fixed operation sets and is designed to perform efficiently with the operation sets. This type of automation is mainly used in discrete mass production and continuous flow systems like paint shops, distillation processes, transfer lines and conveyors. All these processes rely on mechanized machinery to perform their fixed and repetitive operations to achieve high production volumes.
- Programmable Automation:
- Programmable automation systems facilitate changeable operation sequences and machine configuration using electronic controls. With programmable automation, non-trivial programming efforts are required to reprogram sequence and machine operations. Since production processes are not changed often, programmable automation systems tend to be less expensive in the long run. This type of system is mainly used in low job variety and medium-to-high product volume settings. It may also be used in mass production settings like paper mills and steel rolling mills.
- Flexible Automation:
- Flexible automation systems are utilized in computer-controlled flexible manufacturing systems. Human operators enter high-level commands in the form of computer codes that identify products and their location in the system’s sequence to trigger automatic lower-level changes. Every production machine receives instructions from a human-operated computer. The instructions trigger the loading and unloading of necessary tools before carrying out their computer-instructed processes. Once processing is completed, the end products are transferred to the next machine automatically. Flexible industrial automation is used in batch processes and job shops with high product varieties and low-to-medium job volumes.
- Integrated Automation:
- Integrated industrial automation involves the total automation of manufacturing plants where all processes function under digital information processing coordination and computer control. It comprises technologies like:
- Computer-aided process planning
- Computer-supported design and manufacturing
- Flexible machine systems
- Computer numerical control machine tools
- Automated material handling systems, like robots
- Automatic storage and retrieval systems
- Computerized production and scheduling control
- Automated conveyors and cranes
- Additionally, an integrated automation system can integrate a business system via a common database. That is, it supports the full integration of management operations and processes using communication and information technologies. Such technologies are utilized in computer integrated manufacturing and advanced process automation systems.
- Integrated industrial automation involves the total automation of manufacturing plants where all processes function under digital information processing coordination and computer control. It comprises technologies like:
- Fixed Automation:
- Industrial automation is the use of technologies such as computer software and robotics to control machinery and processes which replace human beings in performing specific functions. The functions are primarily centered on manufacturing, quality control and material handling processes.
- Process Automation / Manufacturing:
- Process automation is defined as the use of software and technologies to automate business processes and functions in order to accomplish defined organizational goals, such as producing a product, hiring and onboarding an employee, or providing customer service.
- Process manufacturing utilizes chemical, physical and compositional changes to convert raw material or feedstock into a product. Process manufacturing includes industries such as cement and glass, chemicals, electric power generation, food and beverage, life sciences, metals and mining, oil and gas, pulp and paper, refining, and water and wastewater. Process manufacturing includes both continuous and batch processes.
- Discrete Automation / Manufacturing:
- Discrete automation is the production of parts that are of a quantifiable nature. That may include cell phones, soda bottles, automobiles, airplanes, toys, etc. As you know, an automobile contains many, many parts. The parts required for an automobile are also quantifiable in nature.
- Discrete manufacturing processes include the production of individual parts as well as their assembly into a final product. Discrete manufacturing examples include automobiles, appliances, and consumer electronics.
- Hybrid Automation / Manufacturing:
- The Hybrid Automation Method follows two guiding principles: Implementing robust automation solutions that are easy and affordable for organisations to maintain. Realising process efficiency rapidly by reducing project overheads and time-to-value.
- Hybrid manufacturing is a combination of additive manufacturing (AM) and subtractive manufacturing within the same machine.
- Additive Manufacturing (AM):
- Additive manufacturing is the process of creating an object by building it one layer at a time. It is the opposite of subtractive manufacturing, in which an object is created by cutting away at a solid block of material until the final product is complete.
- Operators across a variety of different manufacturing industries utilize additive manufacturing in various ways. For instance: Medical device manufacturers use 3D printing to develop high variance products such as dental implants.
- The term “additive manufacturing” refers to the creation of objects by “adding” material. Therefore, 3D printing is a form of additive manufacturing. When an object is created by adding material — as opposed to removing material — it’s considered additive manufacturing.
- Smart Manufacturing (SM):
- Technology-driven approach that utilizes Internet-connected machinery to monitor the production process. The goal of SM is to identify opportunities for automating operations and use data analytics to improve manufacturing performance.
- An example of what the cloud can do for smart manufacturing is the Volkswagen Industrial Cloud, which combines all data from 122 Volkswagen Group facilities and processes it in real time to make improvements.
- Mechatronics:
- Mechatronics is a multidisciplinary field that refers to the skill sets needed in the contemporary, advanced automated manufacturing industry. At the intersection of mechanics, electronics, and computing, mechatronics specialists create simpler, smarter systems.
- Mechatronics is the broad term for integrating mechanical, telecommunication, and computer engineering, frequently using microcontrollers.
- Examples of mechatronic systems are robots, digitally controlled combustion engines, machine tools with self-adaptive tools, contact-free magnetic bearings, automated guided vehicles, etc. Typical for such a product is the high amount of system knowledge and software that is necessary for its design.
- Motors, Generators and Drives:
- A motor is the mechanical or electrical device that generates the rotational or linear force used to power a machine.
- An electric motor converts electricity into mechanical energy, providing a power source for machinery.
- A generator does the opposite of this, converting mechanical energy into electricity.
- A servo motor is a self-contained electrical device, that rotate parts of a machine with high efficiency and with great precision. The output shaft of this motor can be moved to a particular angle, position and velocity that a regular motor does not have. It consists of a suitable motor coupled to a sensor for position feedback. It also requires a relatively sophisticated controller.
- A drive (also often referred to as an electric controller) is the electronic device that harnesses and controls the electrical energy sent to the motor.
- By positioning a drive between the electrical supply and the motor, power is fed into the drive, and the drive then controls and regulates the power that is fed into the motor. This allows control of speed, direction, acceleration, deceleration, torque and, in some applications, position of the motor shaft.
- Variable Speed Drive (VSD) – Variable Frequency Drive (VFD) – Inverter:
- A variable speed drive is a device used in electromechanical drives to control the speed and torque of an AC motor by adjusting the motor’s input frequency and voltage. Variable speed drives may be either electric, hydraulic, mechanical or even electronic.
- A Variable Frequency Drive (VFD) is a type of motor controller that drives an electric motor by varying the frequency and voltage supplied to the electric motor. Frequency (or hertz) is directly related to the motor’s speed (RPMs). In other words, the faster the frequency, the faster the RPMs go.
- Other names for a VFD are variable speed drive, adjustable speed drive, adjustable frequency drive, AC drive, microdrive, and inverter.
- An Inverter is a device that converts direct current electricity to alternating current either for stand-alone systems or to supply power to an electricity grid.
- An inverter is one of the most important pieces of equipment in a solar energy system. It’s a device that converts direct current (DC) electricity, which is what a solar panel generates, to alternating current (AC) electricity, which the electrical grid uses.
- Most inverters are installed and used in conjunction with a battery bank of some sort – a common set up in off-grid solar installations.
- => A variable frequency drive (VFD) refers to AC drives only and a variable speed drive (VSD) refers to either AC Drives or DC Drives. VFDs vary the speed of an AC motor by varying the frequency to the motor. VSDs referring to DC motors vary the speed by varying the voltage to the motor.
- Extra Low-Voltage (ELV):
- Voltage of 50V or less (AC RMS), or 120V or less (ripple-free DC).
- Low-Voltage (LV):
- The International Electrotechnical Commission (IEC) defines supply system low voltage as voltage in the range 50–1000 V AC or 120–1500 V DC.
- Medium-Voltage (MV):
- Medium-voltage circuit breakers rated between 1 and 35/72 kV.
- High-Voltage (HV):
- The International Electrotechnical Commission define high voltage as above 1000 V for alternating current, and at least 1500 V for direct current.
- Super High-Voltage:
- Is >300kV.
- Ultra High-Voltage:
- Is >1.000kV.
- Intralogistics:
- Intralogistics is the art of optimizing, integrating, automating, and managing the logistical flow of information and material goods within the walls of a fulfillment or distribution center.
- If logistics is defined as moving things efficiently from point A to point B, then intralogistics is a similar but much-expanded concept. It involves, within a distribution centre or warehouse, optimizing and managing the logistical flow of information along with physical materials management.
- Cobots (Collaborative Robots):
- A collaborative robot, also known as a cobot, is a robot that is capable of learning multiple tasks so it can assist human beings. In contrast, autonomous robots are hard-coded to repeatedly perform one task, work independently and remain stationary.
- Intended to work hand-in-hand with employees. These machines focus more on repetitive tasks, such as inspection and picking, to help workers focus more on tasks that require problem-solving skills.
- A robot is an autonomous machine that performs a task without human control. A cobot is an artificially intelligent robot that performs tasks in collaboration with human workers.
- According to ISO 10218 part 1 and part 2, there are four main types of collaborative robots: safety monitored stop, speed and separation, power and force limiting, and hand guiding.
- Autonomous Mobile Robot (AMR):
- Any robot that can understand and move through its environment without being overseen directly by an operator or on a fixed predetermined path. AMRs have an array of sophisticated sensors that enable them to understand and interpret their environment, which helps them to perform their task in the most efficient manner and path possible, navigating around fixed obstructions (building, racks, work stations, etc.) and variable obstructions (such as people, lift trucks, and debris). Though similar in many ways to automated guided vehicles (AGVs), AMRs differ in a number of important ways. The greatest of these differences is flexibility: AGVs must follow much more rigid, preset routes than AMRs. Autonomous mobile robots find the most efficient route to achieve each task, and are designed to work collaboratively with operators such as picking and sortation operations, whereas AGVs typically do not.
- Automated Guided Vehicles (AGV):
- An AGV system, or automated guided vehicle system, otherwise known as an automatic guided vehicle, autonomous guided vehicle or even automatic guided cart, is a system which follows a predestined path around a facility.
- Three types of AGVs are towing, fork trucks, and heavy load carriers. Each is designed to perform repetitive actions such as delivering raw materials, keep loads stable, and complete simple tasks.
- The main difference between an AGV and an AMR is that AMRs use free navigation by means of lasers, while AGVs are located with fixed elements: magnetic tapes, magnets, beacons, etc. So, to be effective, they must have a predictable route.
- Autonomous Case-handling Robots (ACR):
- Autonomous Case-handling Robot (ACR) systems are highly efficient “Goods to Person” solutions designed for totes & cartons transportation and process optimization, providing efficient, intelligent, flexible, and cost-effective warehouse automation solutions through robotics technology.